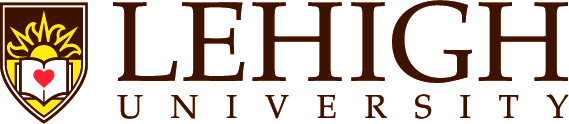
In this episode of Lehigh University’s College of Business IlLUminate podcast, we are speaking with Zach Zacharia about how supply chains are affected by pandemics. Zacharia is an associate professor of supply chain management and director of the Center for Supply Chain Research at Lehigh University where he teaches graduate and undergraduate courses in supply chain and operations management and logistics and transportation.
He spoke with Rob Gerth, director of marketing and communications for Lehigh Business. Listen to the podcast here and subscribe and download Lehigh Business on Apple Podcasts or wherever you get your podcasts.
Below is an edited excerpt from that conversation.
Read the complete podcast transcript.
Rob Gerth: Why is there a lack of toilet paper? Is that a supply chain problem?
Zach Zacharia: I think it's actually related to two things. One is that, first of all, it's a hoarding problem. You get people panicking and going and buying product, in this case toilet paper. And when the demand spikes, you're going to run out of availability. That's always there. One of the things that we need to consider when we take a look at the toilet paper supply chain is really that the companies that make toilet paper serve two large customers. One set of customers are the industrial customers, and the other set is the consumer set of customers. In the consumer market, they are pretty well-aware of the kind of things they need to make, and it's different than what the industrial market is. And that's about a 50/50 split. So when you have a lack of toilet paper, you've got demand that is unpredictable. And toilet paper by itself - let's be clear - it's very bulky. It takes up a lot of space. That's a low-margin item. So if you're a grocery store, you're not going to store a lot of extra toilet paper because demand is relatively constant. Actually this brings this basic idea that in supply chain we try and focus on reducing inventory to be efficient. But there is a thing called the bullwhip effect.
So bullwhip effect by definition is the increasing variability of demand as one moves away from the point of change, as one moves upstream. So let's say you've got a consumer, and the consumer increases their demand by 10%. The retailer seeing that increase in demand is going to order an additional 10%. And the wholesaler who they order from seeing that increase in demand will order an additional 10%, then the manufacturer. And eventually, this goes to raw material supplier. So this demand which started off as a 10% increase could potentially become 40%, and that's a huge difference in demand. So what is key about the bullwhip effect is that this effect has been seen to happen whenever there is distorted information, when there's order batching, there's overreactions, or when there's hoarding. And so the bullwhip effect really happens when people don't share information. So when you look at this example of toilet paper, the question is that could we have predicted that kind of demand? Could we have understood and been prepared for it? Well, you couldn't have because people were hoarding, and people were overreacting to that perceived lack. And it takes a while for a supply chain to be flexible, to change because to add flexibility, it's going to add cost. So the question then is that-- when are you going to have enough toilet paper in every grocery store? Well, when the supply chain has retooled to produce more toilet paper for the consumer market.
Gerth: What about the food supply chain?
Zacharia: This goes also in the food supply chain. Remember, Americans are used to eating about 50% outside the house, be it restaurants, be it school lunches, cafeterias. And when you've taken the demand out of that area, it takes a while for the supply chain to retool because obviously what you are going to sell to a restaurant is different than what you're going to sell to an average consumer in terms of packaging, in terms of the marketing that goes with it. So I think any of these kinds of issues that relate to supply chain-- really has to go to this idea that you design a supply chain to be efficient, to keep it low-cost, and therefore when you make a change, it's going to add a lot of additional cost in the system. And a grocery store doesn't make much money on toilet paper. It's a low-margin item, and it's a big, bulky item. So you're not going to keep a lot of it. You'd much rather have more pasta or bread that people are going to buy and have a little bit more margin and take a lot less space.
Gerth: Obviously pandemic disrupts supply chains. What are some other things?
Zacharia: There's a lot of different things that could potentially disrupt the supply chain, but the top seven sort of supply chain disruptions that as a supply chain professional you're going to actually plan for-- the top seven in the last 10 years, in order of priority, the most disruptive is something related to unplanned information technology or telecommunication problems. That is the number one reason you could have a disruption that information didn't get across. Second is adverse weather. For example, it could be just as simple as a storm to something as severe as a hurricane. But weather issues can affect the delivery of the product to its final destination. There's something wrong with the transportation network that's bringing the product; for example, a port strike or actual problems in the infrastructure and getting that product through. If the third party, the 3PL as you were, the company that actually transports the product has a problem. If you don't have the right kind of people available to be able to work in your supply chain, that's number five. Number six is a cyber-attack or data breach. That's a sixth kind of disruption. The seventh one is new laws or regulations. For example, tariffs that came across affected the supply chain. So those are the top seven supply chain disruptions in the last 10 years.
Gerth: Do companies plan for this?
Zacharia: One of the things that we do in supply chain that's important is to be able to manage even when there is a disruption. And I want to distinguish from those disruptions that we could plan for versus unplanned events. So things that we can plan for are those seven supply chain disruptions, things like adverse weather. We know when a hurricane is coming, and we can actually plan what to do when there is a hurricane. However, there are some kinds of disruptions that are so unique that we actually call them black swan events. And by that I mean is something that is unpredictable and has a potentially severe consequences for the supply chain. And here is the point. You don't plan for black swan events. You basically react. So I want to distinguish between disruptions you can plan for and that you could build redundancies in-- you could say that, "Hey, if the hurricane comes in from this side, I know the first things people need, first responders, they need water." That's something that is really, really critical. So you can get bottles of water available. You can get flashlights. You can actually plan for these kinds of things, and your supply chain can survive in these kinds of situations. However, black swan events are things you can't plan for because that's the whole point. It is something completely unpredictable. And what you really need to do in that case is just simply react and be capable, be flexible in your supply chain.
Gerth: And how long do you think it will take to fix the supply chains?
Zacharia: Well, that again could be that example of that bullwhip effect, right, where all of a sudden, you have increasing demand. And then everyone gets a surplus, and you get decreasing demand. And the way to counteract that is by sharing information. You tell them what the demand actually is. But you're actually right, that there is going to be some inertia in the system. You can't start these things in full speed. Even though the manufacturing plants have started in China, the steamship lines that actually send the container ships that can get that product, they've taken out significant number of their sailings. They've just idled those ships because you don't have enough demand. So it's going to take a while for those companies to start putting those ships out to pick up those containers. So there is going to be some inertia in this whole process, and the problem is there's going to be a little bit of overshooting. Do you prepare for customers to come back into your store? And if those consumers don't come back, what do you do? Let's take the oil as an example. I'm sure you saw that the futures market in oil was for a brief day there trading negative implying that if you drive to a gas station, they're going to pay you money to take that [laughter].
Zach Zacharia, Ph.D., director of the Center for Supply Chain Research at Lehigh University explains why we are having shortages of goods since the outbreak of COVID-19 and potential solutions.